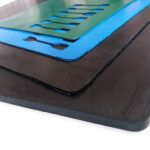
Moulage de plaques
15 décembre 2023Le moulage du caoutchouc est un process de fabrication qui consiste à transformer de la matière caoutchouc plus ou moins souple, en une pièce de forme. SDCM GIROUD est capable de formuler et de produire en interne la matière qui sera utilisée pour réaliser vos pièces de forme sur mesure. Pour cela, l’industrie du caoutchouc a fait évoluer ses techniques et ses équipements, pour répondre à une exigence de qualité toujours croissante.
Aujourd’hui, le moulage d’une pièce s’effectue selon 3 principales méthodes :
– compression caoutchouc : on ferme le moule sur une ébauche du mélange préalablement placée dans l’empreinte,
– compression transfert caoutchouc : la matière est placée dans une cavité auxiliaire appelée pot de transfert ou chambre de transfert, elle est ensuite transférée dans l’empreinte par la force de fermeture du moule,
– injection caoutchouc : le moule et l’empreinte étant fermés, le mélange est injecté dans l’empreinte du moule par la pression du piston d’injection de la presse
SDCM GIROUD vous explique les différentes techniques mises en œuvre dans ses ateliers pour la compression caoutchouc et l’injection caoutchouc, leurs avantages et inconvénients ainsi que les différentes applications.
Moulage par compression caoutchouc : tradition et précision
Le processus de moulage par compression, ancré dans la tradition du caoutchouc, reste une méthode incontournable. Le matériau (caoutchouc, composé de caoutchouc, silicone) est directement placé dans la cavité d’un moule chauffé, fermé sous une pression hydraulique. La pièce prend alors sa forme lors de la fermeture du moule. Une fois la vulcanisation terminée et le moule ouvert, la pièce peut être retirée, et tout excès de caoutchouc ou résidu est éliminé lors de l’ébarbage. Le moule est généralement en acier.
Avantages de la technique « compression caoutchouc » :
- Convient aux pièces à géométrie simple
- Adaptabilité aux productions de prototypes et petites séries
- Coûts d’outillage réduits : moule simple en métal, pas de circuit d’injection.
- Temps de mise en production rapide
Inconvénients de la technique « compression caoutchouc »
- Déchet plus important du fait du chargement excessif en matière (plus de bavures)
- Ebavurage plus difficile
- Processus plus lent ; chargement et temps de vulcanisation long
- Coûts de main-d’œuvre plus élevés car automatisation plus difficile
- Risque accru de défauts d’air et de remplissage
Variante du moulage par compression : le moulage par compression transfert
Dans le process de moulage par transfert, plutôt que de placer une ou plusieurs ébauches de matière directement dans chaque empreinte du moule, une seule ébauche est insérée dans le pot de transfert de l’outillage. Le verrouillage de la presse permet l’écrasement de l’ébauche et le transfert simultané de la matière dans les empreintes via des pin points.
Les principaux avantages de cette méthode sont :
- Un temps de vulcanisation de pièce diminué grâce à l’auto-échauffement de la matière lors du passage des pin-points
- Moins de bavures pièces dû au meilleur serrage et au transfert de la seule matière nécessaire
- Alimentation plus rapide d’un grand nombre d’empreintes (1 seule ébauche)
Le principal inconvénient est le volume de déchets important dû à la nappe de transfert (surplus de matière restant dans le pot de transfert et non acheminé dans les empreintes du moule)
Moulage par injection caoutchouc : précis et rapide
Ce procédé consiste à injecter sous haute pression un mélange caoutchouc dans les cavités d’un moule. Le matériau en caoutchouc non vulcanisé est avalé par une vis qui alimente un piston d’injection. Sous la pression hydraulique du piston, ce mélange sera injecté dans le moule fermé comme le ferait une seringue. Après vulcanisation ou cuisson dans le moule chauffé, la vis sans fin se remet en rotation pour remplir à nouveau le cylindre d’injection.
L’injection caoutchouc, méthode moderne et rapide, offre une précision optimale pour la production en série. En effet, l’injection sous pression dans le moule assure un remplissage homogène du caoutchouc et donc une meilleure qualité de pièce en sortie de presse. Le moulage par injection représente la méthode la plus efficiente pour la fabrication de produits en caoutchouc moulé et trouve de nombreuses applications dans des domaines d’activité très variés.
Avantages de la technique « injection caoutchouc » :
- Temps de vulcanisation et de cycles plus courts
- Moins de bavures sur la pièce dû au dosage précis de la matière par la presse
- Nombreuses possibilités de réglage des paramètres de moulage
- Coût de revient plus attractif pour les grandes séries que la compression
- Possibilité d’automatisation plus nombreuses
Inconvénients de la technique « injection caoutchouc »
- Moule plus évolué et plus cher (canaux d’alimentation, mécanismes…)
- Temps de mise en production et nettoyage de l’unité d’injection plus long
Découvrir des exemples de fabrication de pièce en injection caoutchouc SDCM GIROUD
Le surmoulage caoutchouc :
Le surmoulage caoutchouc est un processus de fabrication qui consiste à intégrer un élément constitué d’un autre matériau (insert) dans le moule. Celui-ci sera noyé ou revêtu avec le caoutchouc lors de la phase de surmoulage. Il est possible d’adhériser l’insert avec une colle spécifique pour lier chimiquement les deux matériaux.
Voici les étapes du surmoulage caoutchouc :
- Préparation de l’insert : Tout d’abord, la pièce de base sur laquelle le surmoulage va être effectué est préparée. Cela peut inclure un traitement mécanique (sablage, microbillage …), un dégraissage suivi de l’application d’une colle en mono ou bi-couche pour favoriser l’adhérence du caoutchouc sur l’insert. SDCM GIROUD est équipée d’un atelier d’adhérisation dédié.
- Surmoulage : L’insert est disposé dans l’empreinte du moule avant le cycle de moulage. Le mélange caoutchouc est injecté ou pressé sur l’insert. La pression et la température sont contrôlées pour assurer une adhérence adéquate entre le caoutchouc surmoulé et l’insert. L’agent adhérisant appliqué en amont va vulcaniser avec le caoutchouc lors du surmoulage et ainsi lier chimiquement les deux matériaux.
Les pièces fabriquées par surmoulage caoutchouc sont par exemple : des poignées d’outils, des butées, des silentblocs, des joints d’étanchéité. Ce processus peut être utilisé pour ajouter une fonction à une pièce rigide métallique ou plastique telles que l’isolation électrique, l’absorption des chocs, l’adhérence ou l’étanchéité.
Pièces moulées en caoutchouc : pourquoi choisir l’injection caoutchouc plutôt que la compression caoutchouc ?
La diversité des pièces moulées en caoutchouc et leur importance dans des secteurs aussi variés que l’électrique, le BTP ou les transports imposent une qualité de pièce et finition irréprochables. En effet, les composants caoutchouc jouent un rôle crucial dans la durabilité, la sécurité et les performances des équipements et véhicules. Au-delà des avantages et inconvénients de chaque méthode, c’est la pièce finale et les spécificités techniques recherchées ainsi que les volumes qui vont décider du meilleur process de fabrication.
On s’entend à reconnaître que le processus de moulage de caoutchouc, qu’il soit par injection caoutchouc ou compression caoutchouc permet une grande souplesse dans la conception des pièces. De ce fait, il permet de produire des composants et ensembles aux formes complexes et géométries variées.
SDCM GIROUD saura vous accompagner dans le choix de la méthode adaptée (injection ou compression caoutchouc), selon la forme de la pièce à produire, les matériaux utilisés, les volumes attendu et surtout la fonction de la pièce.
Compression caoutchouc, injection caoutchouc : choisir le bon partenaire
Avec 73 ans d’expérience en fabrication de pièces en caoutchouc moulé et un parc machines dernière génération, en compression caoutchouc, compression transfert caoutchouc, injection caoutchouc, SDCM GIROUD est un partenaire fiable et expérimenté, pour vous accompagner dans vos projets.
- Son laboratoire interne formule pour vous un mélange sur-mesure pour répondre aux contraintes d’utilisation de votre pièce, par exemple résistance aux UV, aux huiles, à l’abrasion, adhérence, allongement, isolation etc
- L’atelier de fabrication produit la matière formulée sur ses mélangeurs à cylindres
- Le bureau d’étude vous accompagne dans les phases d’optimisation géométrique, de conception du moule et de prototypage
- Le parc machine récent vous assure une production de vos pièces de qualité tout en respectant vos contraintes économiques
- Son service ébavurage cryogénique permet une grande qualité de finition de vos pièces.
Autant d’atouts décisifs pour trouver votre partenaire !
Un conseil ? Un projet ? N’hésitez pas à nous contacter :
au 04 76 36 40 66 ou par mail info@sdcmgiroud.fr.